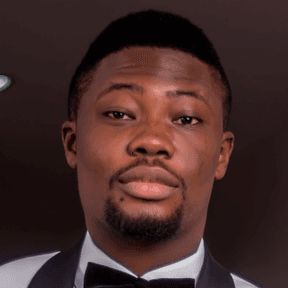
Adeyemi Adesina
Market Quality Improvement and Performance Manager at Nestlé
Master of Business Administration (MBA) at Nexford University
Nigeria
Get Remote-Ready with the Anywherepro Assessment
Increase your chances of landing your dream hybrid or remote job today!
Earn your badgeHi, I'm Adeyemi Adesina!
Market Quality Improvement and Performance Manager at Nestlé
Highly motivated and result driven Quality Manager with a proven track record of implementing TPM Q-Pillar, GLOBE Quality Management, Food Safety and Quality Management Systems, and audits. Seeking a challenging position in which I can utilize my expertise in quality assurance, process improvement, and regulatory compliance to drive continuous quality enhancement and ensure customer satisfaction.
Experience
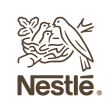
Market Quality Improvement and Performance Manager
December 2021 - Present
- Lead the implementation of the Q pillar methodology, conducting root cause analysis and implementing corrective actions to eliminate defects and improve quality performance in the market.
- Managed and ensured compliance with Food Safety and Quality requirements, including HACCP principles, GMPs, and regulatory standards, for finished products in factories.
- Managed and coordinated the implementation and maintenance of Quality Management processes on SAP, ensuring data integrity and streamlined quality operations across the market.
- Implemented training programs, workshops, and knowledge-sharing sessions to enhance technical competencies among market specialists. This facilitated the acquisition of new skills and knowledge, enabling them to drive quality improvements effectively.
- Implemented problem-solving training programs and provided coaching to enhance problem-solving competencies among market teams. This led to improved problem-solving skills and the ability to address quality issues proactively.
- Consistently driving quality system continuous improvement programmes that are centered on what the consumer values (including defect elimination, efficiency increase, and process optimization).
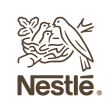
Quality Improvement and Compliance Coordinator
August 2020 - December 2021
Analysed food safety data and generated reports to identify trends and opportunities for improvement.
Conducted regular food safety audits and inspections to identify potential risks and areas for improvement.
Consistently ensured regulatory and internal compliance of food, adhering to requirements related to contaminants (e.g., SON, NAFDAC and CODEX standards), physicochemical properties, and microbiological safety (e.g., HACCP principles)
Managed SAP QM applications, facilitating the timely release of finished goods, ensuring adherence to quality system standards on SAP, and implementing robust business continuity measures.
Managed the defect elimination and reduction journey, utilizing problem-solving tools such as 4M analysis, DMAIC, and 5 Whys. This resulted in an 85% decrease in defects and progress towards achieving Zero defect status.
Continuously optimized the Quality management process by digitalizing workflows such as document control, non-conformance management, and corrective actions. This reduced activity time by 70%, eliminated paper-based processes, and improved information storage and retrieval efficiency.
Actively participated in quality initiatives, collaborating cross-functionally to ensure the successful launch of new products with rigorous quality checks and supporting continuous improvement efforts for existing products.
Prepared for and participated in regulatory audits, customer inspections, and internal inspections to ensure compliance with quality standards and regulatory requirements. Also led internal inspections to drive continuous improvement and adherence to quality systems.
Implemented KPIs to monitor QA systems, such as on-time usage decision, first time right, and customer complaint resolution time. These KPIs drove efficiency by improving delivery timelines and reducing defects, while ensuring compliance with quality standards.
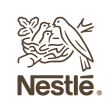
Quality Systems Specialist
January 2015 - July 2020
Ensured elimination of defects by engaging people systematically in the use of TPM Q-Pillar problem-solving methodologies and tools.
Participated in the development and implementation of HACCP and Food Safety Management programs.
Created systems to optimize work time, reduced time to document GMP audit gaps by 70%, and implemented an easy system to capture and address complaints, resulting in a 20% reduction in defects.
Managed compliance of incoming materials to contaminant requirements, improving the quality and food safety of finished products, especially grains. Implemented cost optimization strategies, resulting in optimized cost of quality.
Introduced digital systems for immediate management of food safety and quality issues on the shop floor, enhancing response time and efficiency.
Achieved compliance with food safety and quality standards through active participation in NIA internal assessments.
Simplified HACCP processes in the factory, streamlining and improving effectiveness.
Ensured SAP QM compliance with quality and food safety requirements, leading to a satisfactory Nestlé Internal Audit rating for Agbara Factory.
Implemented reduced inspections to optimize the cost of analyzing incoming goods, resulting in cost savings of CHF30,240.25 between January and April 2021.
Led the implementation of Process Release in two factories, contributing to estimated annual cost savings of CHF161,039.
Implemented GLOBE LIMS for the Regional Microbiology Laboratory, improving laboratory efficiency in reporting.
Led the team to successful implementation of ISO 9001:2015 and FSSC 22000 in the factory, ensuring compliance with international quality standards.
Played a key role in the successful launch of MILO RTD and CERELAC Care products, including NAFDAC and FDA Ghana audits.
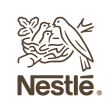
Quality Assurance trainee
December 2011 - December 2014
Sampled and carried out microbiological, and chemical analysis of raw materials (ROH), semi-finished and finished products.
Carried out document control for the factory and in addition, devising and establishing a company's quality procedures, standards, and specifications.
Certificates & Badges
No certificates or badges added
Projects
No projects added
Languages
English
Skills
Problem Solving
Microsoft Office
SAP
Quality Control and Assurance
Quality Auditing
ISO
Food Safety
Total Productive Maintenance (TPM)
DMAIC